Programmable Logic Controllers, or PLCs, are a type of industrial computer system used to control machines and processes. They provide a reliable, efficient means of automating operations in a variety of industries, such as manufacturing and process control. PLCs are typically used in hazardous environments or where precision is required. They are also commonly used in robotics, power plants, and other industrial applications.
PLCs Basics
Programmable Logic Controllers (PLCs) are versatile devices used to control industrial equipment and processes. They offer automation, reliability, and flexibility to operations in a wide range of industries through their advanced programming capabilities. For those new to PLCs, understanding the basics will help you get started.
PLCs are electronic devices that use instructions stored in memory for operating various types of automated machinery. This includes motor controls, conveyors, pumps and other automated processes. A PLC can be programmed using various languages including ladder logic diagrams or instruction lists & scripts written in computer language such as C++ or Java. The user can input data from sensors into the programmable logic controller which can then process and store information before sending out commands accordingly.
History of PLCs
Programmable logic controllers (PLCs) are an essential tool for many industrial automation and data-driven processes. Throughout the years, PLCs have evolved from simple relay control systems to sophisticated systems that can facilitate seemingly limitless industrial applications.
The first digital computers were developed in the 1940s, but it wasn’t until 1969 when General Motors Corporation created the very first programmable logic controller (PLC). Invented by engineer Dick Morley, this device was designed to replace traditional electromechanical relays with a more efficient system. The PLC achieved this efficiency by using computer programming language to be able to automate complex sequences of functions. This invention revolutionized industrial automation processes and enabled humans to take on more difficult tasks instead of handling mundane activities.
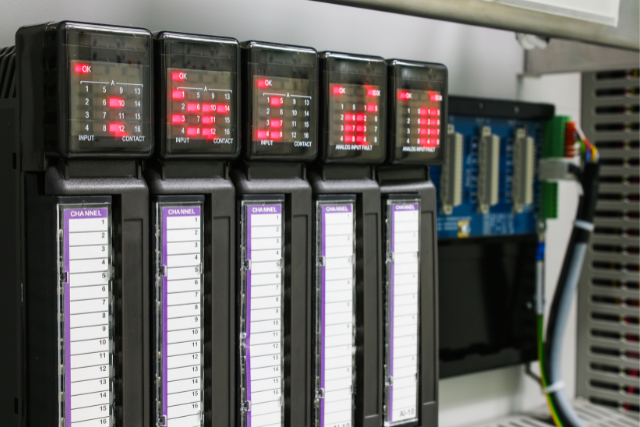
Major players in PLC industry
A few major players have emerged as leaders in the PLC market, setting standards and offering cutting-edge technology to customers around the world.
Allen-Bradley
Allen-Bradley is a leading provider of programmable logic controllers (PLC) and automation solutions. With over 100 years in the industrial automation industry, Allen-Bradley has developed a broad range of reliable and user-friendly products. Their PLCs are designed to maximize production efficiency while providing secure data management and control systems.
The Allen-Bradley ControlLogix family of PLCs offers advanced features such as motion control, safety integration, process control, energy management, remote access capabilities and more. The company also provides an array of software tools for programming, configuration, monitoring and diagnostics. This allows users to quickly configure complex applications with ease. Additionally, the integrated architecture offers modularity for future expansions or upgrades with minimal effort needed for reconfiguration or maintenance.
Siemens
Siemens is a German-based multinational industrial manufacturing company that has been in operation since the mid 1800s. The company is well known for their programmable logic controllers (PLCs), which are used to automate a variety of processes within industrial settings. Siemens PLCs have become a mainstay in modern factories and production lines, thanks to their advanced programming capabilities and high reliability.
In addition to being highly reliable, Siemens PLCs are also very user friendly and offer powerful programming tools that make it easy for operators to configure them for various tasks. They can be set up with custom logic equations or pre-programmed into various modes, making them extremely versatile. Furthermore, they’re designed with safety mechanisms to protect both workers and equipment from damage due to faulty operations.
AutomationDirect
AutomationDirect is a leading provider of PLCs, offering a wide range of solutions to meet the needs of virtually any application. With products ranging from entry-level models to sophisticated systems with advanced features, AutomationDirect offers unparalleled solutions for managing complex operations.
The company’s comprehensive selection includes low-cost logic controllers for basic automation applications and high-end controllers designed for demanding production environments with large amounts of data processing requirements. Their product line also includes Ethernet I/O modules, motion control cards, communication cards, power supplies, and other accessories needed to fully customize the system. All these components are rigorously tested by AutomationDirect’s experienced engineering team to ensure quality performance over long periods of time.
Omron
Omron is one of the leading manufacturers of programmable logic controllers (PLCs). PLCs are used to automate and control industrial or commercial processes. Omron’s PLC systems are incredibly reliable, cost effective, and easy to use. Omron has an extensive lineup of products that provide flexibility for users, including a wide range of I/O modules, communications protocols and even specific industry variants. These features make it suitable for many different applications from small-scale automation projects to large scale integrated manufacturing systems.
Omron’s product line also offers advanced features like motion control capabilities, Ethernet connectivity and multiple programming languages for developers. This ensures that customers get exactly what they need in terms of performance and functionality. Furthermore, Omron provides software support as well as training courses to help ensure users get the most out of their PLC systems.
Rockwell Software
Rockwell Software is a leading provider of programmable logic controllers (PLCs) and automation solutions. The company has been providing reliable and cost-effective PLCs to businesses around the world for decades. Rockwell Software prides itself on its innovative engineering, advanced technology, and highly skilled personnel that are dedicated to helping customers increase efficiency and maximize productivity in their operations.
The Rockwell Software PLC range offers an extensive selection of products designed for use in a wide range of applications from automotive production lines to pharmaceutical manufacturing processes. Each model features robust construction, efficient operation, user-friendly programming software, and easy integration with other systems. With these powerful yet economical solutions, customers can be sure they are getting the best value for their money when they choose Rockwell Software’s PLCs.
Schneider Electric
Schneider Electric is a global leader in energy management and automation solutions. Through their commitment to innovation, the company has developed a wide range of programmable logic controllers (PLCs) that are ideal for today’s automation system requirements. Schneider Electric PLCs provide reliable performance and can be easily integrated into different applications. With built-in safety functions and secure communications, Schneider Electric PLCs allow users to automate their processes with confidence.
The wide selection of Schneider Electric PLCs offers a number of advantages such as improved system reliability and efficiency, flexibility to customise systems according to specific requirements, environmental compliance, scalability & compatibility across different platforms and industrial protocols plus fast commissioning times & remote monitoring capabilities. The company also provides technical assistance along with installation & maintenance services for its products ensuring that customers have access to reliable support when needed.
Components of a PLC
Programmable Logic Controllers (PLCs) are an essential part of industrial automation, and understanding their components is key to efficient and effective use. PLCs are composed of a few main parts: the CPU, I/O modules, programming software, power supply, enclosure, and communication interfaces.
CPU
The CPU, or central processing unit, is the “brain” of a PLC system; it takes input from sensors and other devices to decide what outputs should be sent. This includes making decisions about when motors should turn on or off, when valves should open and close, and more.
The CPU is typically located within the main PLC housing unit but can also be connected externally via wiring to create a distributed system where multiple CPUs work together for more complex tasks. The CPU itself consists of several parts including memory chips which store instructions for the controller to follow as well as input/output ports which connect it with external devices like transducers and sensors.
I/O Modules
One of the key components of a PLC is its input/output (I/O) module. The I/O modules connect the physical inputs and outputs to the system itself; these usually include digital inputs such as buttons or switches as well as analog inputs like thermometers or pressure gauges. Outputs may consist of things like motors for actuation or lights for signaling. By using I/O modules, it is possible to quickly configure physical devices with the PLC, allowing for rapid changes in operation without having to reconfigure every component individually.
Programming software allows users to customize their PLCs by writing code that defines how they will operate under various conditions. This allows them to create complex automated systems that require minimal human intervention. Additionally, programming software also makes it easier for engineers and technicians to diagnose any issues that may arise with their PLCs so they can quickly identify and fix any problems.
Power supply
Power supply is a vital component of any Programmable Logic Controller (PLC) system. Without an adequate and reliable power source, the PLC will not be able to control or monitor processes in a timely manner, leading to costly downtime for businesses. In order for PLCs to operate properly, they must have a consistent source of voltage and current as well as appropriate protection from electrical surges.
The most common type of power supply used with PLCs is AC/DC converters since they are both cost-effective and easy to integrate into existing systems. However, not all AC/DC converters are suitable for use with PLCs due to their wide range of inputs and outputs. It is important that users understand the specific requirements of their applications before selecting the right converter in order to ensure optimal performance while avoiding any potential damage caused by incorrect power supplies.
Enclosure
A properly designed enclosure will provide protection from dust, water and other elements, while also allowing for proper ventilation that keeps the system running efficiently. Enclosures come in many different shapes, sizes and materials to suit various applications and environment conditions. An aluminum enclosure may be used in an outdoor setting to protect against corrosion and UV damage, while a stainless steel enclosure is better suited for areas with higher levels of moisture or chemicals present. Depending on the application, there are also custom enclosures available that can meet specific requirements for size or material type.
Communication interfaces.
Programmable Logic Controllers (PLCs) are designed to help manage complex industrial processes, but for the technology to be effective and reliable, it must be properly integrated into a system. This integration relies on effective communication interfaces that can link PLCs with other devices in the system.
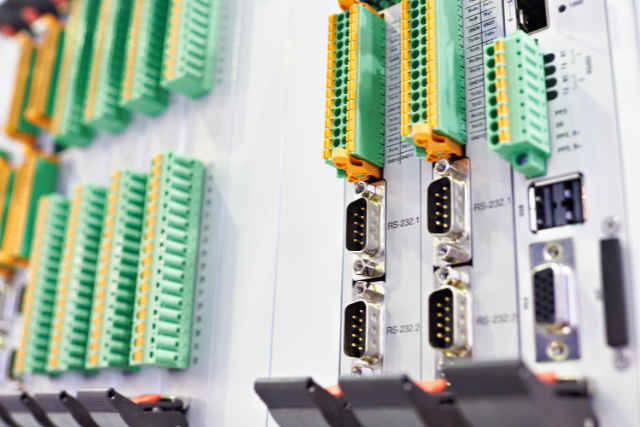
The choice of communication interface is determined by the environment, data throughput needed and existing systems already in place. Common communication protocols used by PLCs include Ethernet/IP, Modbus TCP/IP, CANopen and more recently OPC UA. Each protocol has its own unique features and advantages depending on the type of application being implemented. For example, Ethernet/IP is suitable for real-time applications requiring precise control over timing while OPC UA provides support for a wide range of objects including sensors and actuators, with additional security features such as authentication or encryption.
Types of PLCs
Programmable Logic Controllers (PLCs) are computer-based controllers used in industrial automation processes. They offer features such as automated data collection and control of electrical systems, providing the flexibility and efficiency needed to streamline production. Several types of PLCs are available, each with its advantages and disadvantages.
Compact PLCs
Compact PLCs are an increasingly popular type of automation solution for industrial systems. These powerful yet small controllers are becoming a powerful tool in the manufacturing, packaging, and process industries, providing users with numerous advantages over traditional larger Programmable Logic Controllers (PLCs). Due to their small size, compact PLCs offer flexibility, scalability, and cost savings. They can also be used in tight spaces where larger, traditional PLCs can’t fit. They also have improved programming capabilities and intuitive and user-friendly software for simple setup and operation.
Also, compact PLCs can offer faster response times and better system performance because they process data quickly. Their integrated communication ports allow networking with other devices, such as sensors, switches, or motors on the same network, making them ideal for distributed control applications.
Modular PLCs
Modular PLCs are an increasingly popular choice for automation solutions. In the past, these computers were large and expensive, making them out of reach for smaller businesses and those with tighter budgets. But now modular PLCs offer more features than ever before at a fraction of the cost.
Their flexibility is unparalleled: they can be easily connected to new devices, sensors, and controllers. The ability to be customized in terms of power supply, memory, I/O size, communications capability, and other features make them ideal for businesses that need reliable performance but don’t have the budget or resources to purchase a larger system. Their advanced programming capabilities can be tailored to fit any application- controlling a production line or managing manufacturing processes.
Stackable PLCs
Stackable PLCs are an increasingly popular option for automation solutions. They offer more flexibility than traditional programmable logic controllers (PLCs) and can be used to control various processes, from small machines to complex systems. Stackable PLCs are modular, allowing users to build upon the existing architecture by adding additional modules as needed. This makes them ideal for quickly adapting to changing production demands or incorporating new technologies into existing systems.
The ability of stackable PLCs to ‘stack’ – or link together – different components makes them especially useful when dealing with multiple machines or processes that traditionally require a single, large-scale solution. By using several smaller stackable PLCs, users can achieve the same level of control over their operations but at a reduced cost and with greater flexibility.
Distributed Control Systems (DCS)
Distributed control systems (DCS) are a powerful tool for automation solutions. This technology is used across many industries, from manufacturing and energy production to transportation and communications. DCS provides various benefits, such as improved safety and cost savings. It also offers real-time monitoring of equipment performance and procedural compliance.
The DCS system consists of controllers, input/output devices, software applications for process control and data acquisition, and networked computers for data analysis and decision-making support. This setup allows for more efficient operations and greater flexibility in responding to changing processes or conditions on the production floor. With advanced features like distributed process control integration, remote access capabilities, fault detection, and alarm management tools, DCS can be tailored to meet the needs of any application or industry it is used in.
Programmable Automation Controllers (PAC)
Programmable Automation Controllers, or PACs, are an increasingly popular choice for automation solutions. PACs are designed to facilitate the programming and control of industrial machines. PACs offer a wide range of features to make the process easier and more efficient. These controllers provide a flexible and reliable platform for complex control applications with high-speed data processing capabilities, making them ideal for modern automation needs.
PACs are highly versatile devices that can be programmed using programming languages such as ladder logic, C/C++, Java or Visual Basic to create automated systems that can handle various tasks. They offer increased flexibility over Programmable Logic Controllers (PLCs) in terms of their ability to integrate with other systems, such as SCADA and HMI networks, while also providing higher levels of closed-loop control over processes like robotics and motion control systems.
Advantages/Disadvantages
Programmable Logic Controllers (PLCs) are a type of industrial automation device used to control various processes in the manufacturing and production industry. PLCs offer many advantages when it comes to handling complex automation tasks, but some drawbacks must be considered.
The main advantage of using PLCs is their flexibility. Unlike traditional controllers, they can be programmed to do different actions depending on the situation. This allows them to handle multiple tasks and processes simultaneously, making them ideal for complex production lines where all components must work together correctly. Additionally, PLCs provide faster response times than other controllers since their programming can be changed quickly and easily.
However, there are also some drawbacks associated with PLCs that must be taken into consideration before installing one. For example, their high price makes them an expensive option. In addition, PLCs are limited in that they can only be programmed by those with the necessary skills, which may not be available at a particular facility or may require an expensive and lengthy training program.
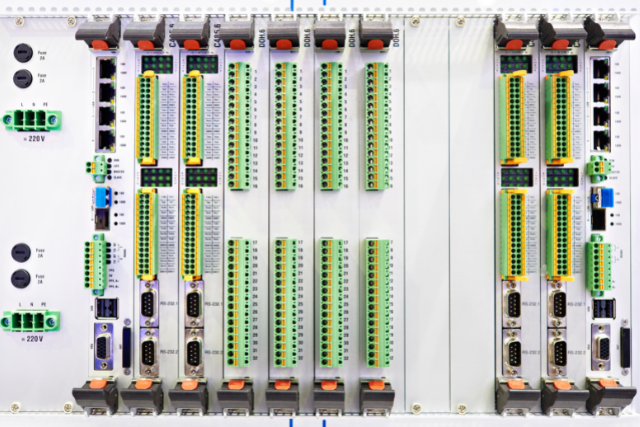
Selection criteria for PLC
Programmable Logic Controllers (PLCs) are a popular choice for industrial control applications due to their high reliability and ease of use. Their effectiveness in controlling various processes makes them an excellent choice for modern production environments. But selecting the suitable PLC is not always easy, as a wide variety of options are available on the market.
Desired Features and Capabilities
When choosing a PLC, the first step should be to determine the desired features and capabilities that it must have so that it can successfully meet your process requirements. Some critical criteria include power source, operating voltage, input/output capabilities, memory capacity, and communications protocols.
Power source
As their main source of power is electricity, PLCs offer cost-effective energy efficiency when compared to other automation solutions. This makes them ideal for businesses that require a reliable yet affordable means of automating tasks or manufacturing processes.
The power requirements for a single PLC can be minimal, especially when compared with traditional industrial control systems using hardwired circuit boards and relays. In addition, PLCs operate with extreme accuracy and speed without any additional energy costs required. This helps businesses to save money on operational costs while increasing productivity levels across the board. Furthermore, since these controllers do not require frequent maintenance or replacement due to wear or tear, they can last many years with little upkeep required from the user.
Operating voltage
A key factor that determines performance is the operating voltage of PLCs, which can vary depending on the application. Operating voltage refers to the power supply used by the PLC, typically ranging from 12-24 volts DC or 110-240 volts AC. The specifications for each device must be considered when determining an appropriate operating voltage for a given application; some devices will have higher current requirements than others, and therefore require more voltage to run properly. Additionally, certain applications may call for special voltage levels such as 48 VDC or 24 VAC/VDC hybrid solutions.
Input/output capabilities
PLCs provide incredible input/output capabilities and are designed to function as an interface between the control system and its physical environment. Boasting flexibility, scalability, and reliability, these controllers can communicate with various types of devices such as sensors, actuators, relays, motor starters, valves and switches.
PLCs have been programmed to interpret analog signals from pressure transducers or vibration sensors for monitoring machines in order to detect any signs of unusual behavior. Additionally they are capable of controlling complex motion paths using pulse-width modulation techniques while also providing fast response times when performing actions like emergency stop operations or fault resets.
Memory capacity
PLCs offer superior storage capabilities compared to other computer systems and can support up to 256K of memory in some models. This allows operators to easily store large programs and data for use by the control system. The internal memory also provides better protection against power outages or other issues as all programs are stored within the PLC making it highly reliable. In addition, many PLCs have various types of external storage such as removable flash drives, allowing users to enhance their existing systems without having to replace them entirely.
Communications protocols
These are an integral part of the automation industry. Programmable Logic Controllers (PLCs) can be programmed to perform various tasks, from controlling and monitoring automated processes to executing data-driven operations. To maximize the effectiveness of these systems, they must be able to communicate with other devices or systems. This is where communication protocols come in; they provide the necessary connectivity between different devices, allowing them to share information and control each other.
The most commonly used protocol in PLCs is Modbus, an open standard for connecting automation devices such as sensors and controllers that use serial protocols like RS485 or Ethernet. Modbus allows PLCs to interact with external components, allowing users to create sophisticated automated solutions tailored precisely for their needs. With Modbus, users can take full advantage of the power and flexibility offered by PLCs. By harnessing the potential of this reliable protocol, businesses can save time and money while optimizing processes and operations within their organization.
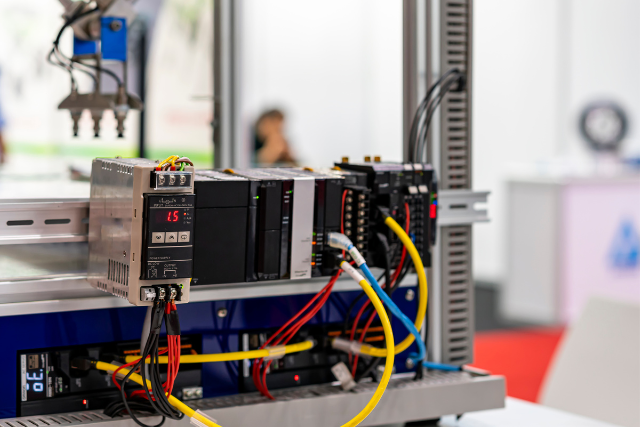
Assessing the Quality of a PLC
Assessing the Quality of a PLC is essential for companies that need the utmost reliability and accuracy from their Programmable Logic Controllers (PLC). It’s essential to consider several factors when assessing a PLC’s quality, such as its design, construction, and programming. A suitable PLC can help improve production efficiency and reduce downtime on industrial applications.
When evaluating a PLC, it’s essential to look at its design features. Are there robust safety features? Does it have multiple communication ports? Is it easy to program? These are all important questions that should be asked when assessing the quality of a PLC. You should also consider the construction materials used in making the device – is it made with durable metals or plastics that won’t wear down quickly over time?
Meeting safety and regulatory standards not only keeps workers safe but also ensures that your system is compliant with relevant industry codes and regulations. Additionally, meeting these requirements will ensure that your PLCs are running properly and efficiently resulting in better overall performance from your system.
Safety standards vary by country; however, some of the most common include: National Fire Protection Agency (NFPA), Underwriters Laboratories (UL), Canadian Standards Association (CSA) and International Electrotechnical Commission (IEC). It’s essential to research which ones apply to you when selecting a PLC or making changes to an existing one.
Evaluating the Cost of a PLC
Programmable Logic Controllers (PLCs) are powerful tools to automate and manage industrial processes. They can be expensive, however, so businesses need to determine if the cost of a PLC makes sense for their operations. Evaluating the cost of a PLC will involve assessing the potential risks associated with manual processes and analyzing how much time and money can be saved by using automated technology.
When deciding on an appropriate PLC for a given application, it is essential to consider all available features and price points. The amount of input/output (I/O) required should also be considered when deciding which type of controller to buy since each model has its capacity limit. Additionally, some systems may require hardware or software upgrades to function appropriately within specific environments.
Understanding User Requirements for a PLC
When designing a programmable logic controller-based system, it’s essential to understand what type of inputs and outputs will be used and if any additional control modules or components need to be included to meet the desired functionality of the system. Additionally, certain types of instructions may be needed depending on the application, such as pulse width modulation or motion control algorithms.
Taking into Account Support Services Offered by the Manufacturer
When selecting a suitable unit for your business needs, it is essential to consider the support services offered by the manufacturer. Doing this can help ensure you have access to the best possible tech support and maximize your investment when purchasing a PLC.
When looking for a service provider for your PLCs, ensure they offer online technical support and user-friendly manuals and tutorials. Additionally, inquire about training programs that may be included in the purchase of a new unit. This will ensure you know how to use and maintain your new product correctly. Lastly, look into warranty information such as what replacement parts come with purchase and what other repair options are available if needed.
Once the desired feature set has been determined, it’s time to compare and evaluate the PLCs that can meet your requirements.
Applications of PLCs
Programmable logic controllers (PLCs) are highly versatile, microprocessor-based devices that control and automate industrial machinery and processes. They are commonly found in manufacturing plants, factories, and other industrial environments where accurate, reliable automation is necessary for optimal performance.
PLCs in Automation
By using a combination of digital inputs and outputs, as well as analog inputs and outputs for monitoring or controlling analog signals like temperature or pressure levels, PLCs can be programmed to do complex tasks automatically with little human intervention. This makes them ideal for use in such diverse industries as manufacturing, oil & gas production, and water treatment facilities.
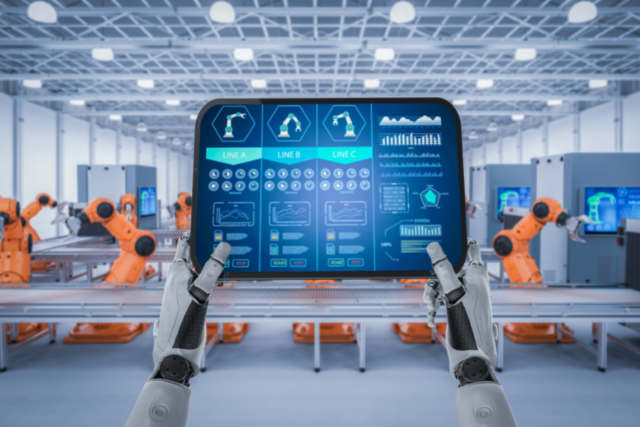
PLCs in Industrial Process Control
Programmable Logic Controllers (PLCs) have become an essential tool for industrial process control. These controllers are used in a variety of commercial and industrial applications, including manufacturing, machine automation, automotive production processes, and more. PLCs provide an automated approach to controlling these processes by combining logic functions with programmable memory.
The use of PLCs provides many advantages over manual operation of industrial processes. For example, they are faster than manual operations and can be programmed and reprogrammed as needed to accommodate changes in the environment or new requirements. Additionally, they are reliable—minimizing downtime due to mechanical malfunctions or human errors—and cost-effective when compared to other solutions such as hardwired systems or dedicated computers.
PLCs in Robotics
With a PLC, robotic systems can be programmed to perform a wide range of tasks quickly and efficiently. PLCs provide users with a number of benefits, from increased safety to enhanced accuracy and flexibility.
The application of PLCs in robotics offers many advantages over traditional methods of automation. PLCs allow robots to respond more accurately and effectively to changes in their environment, providing greater control over the robot’s motion. In addition, they enable robots to carry out complex tasks with minimal human intervention by allowing them to be pre-programmed and set up prior to activation.
PLCs in Networking and Communication
From networking and communication to monitoring processes and controlling equipment, PLCs are tremendously versatile when it comes to handling complex automation tasks. In the world of networking and communication, PLCs offer an array of options for linking machines together.
With their ability to capture data from various sources such as sensors and other devices, they can be used to communicate between systems in order to simplify coordination across multiple sites. Additionally, their high-speed processing capabilities enable real-time analysis of large volumes of data for improved decision making. This makes them an invaluable asset when it comes to managing complex networks with multiple nodes interconnected over long distances.
PLCs for Safety and Security
PLCs offer some of the most reliable solutions available to protect people, property, and information. Integrating PLCs into a safety or security system is often done by linking them up with other devices such as sensors, alarms, and cameras. Once connected, the PLC can be programmed to detect changes in the environment or certain events which can then be used to trigger a response.
This could range from sending an alert message to disabling specific systems or locking down areas when necessary. With their unparalleled precision and flexibility, it’s no wonder why PLCs are so widely used in safety and security contexts.
PLCs for Monitoring and Diagnostics
Programmable Logic Controllers (PLCs) can provide a wealth of solutions for monitoring and diagnostics. PLCs are popular for their real-time control capabilities, accuracy and efficiency in managing the production line, but their use is often overlooked when it comes to diagnostics and preventive maintenance.
With a PLC system installed, users can access data collected from various points on the machine network which can be used to quickly diagnose problems as they arise. The onboard diagnostics features allow operators to identify exactly where problems lie within the system without having to physically inspect each component of the machine. This makes it ideal for troubleshooting purposes as it allows engineers to quickly isolate any issues that may be occurring in order to prevent any further downtime or disruption of productivity.
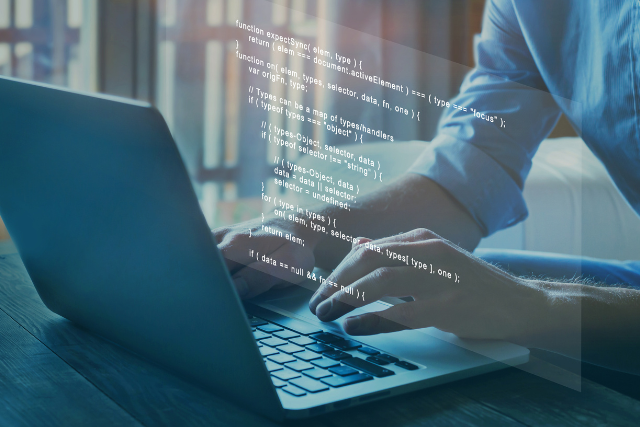
Conclusion
Programmable Logic Controllers, or PLCs, provide various advantages over traditional controllers. They are more reliable, require less maintenance, and allow for greater flexibility in automation setup. With these facts in mind, it can be concluded that PLCs are an excellent choice for many industries and applications.
The primary benefit of using PLCs is their cost efficiency; they substantially reduce operating costs compared to other types of controllers. Additionally, the programming language used by most models is easy to learn and understand.
This simplifies the configuration process significantly compared to other controllers that require specialized programming knowledge. Finally, the high level of accuracy offered by PLCs makes them ideal for precision tasks such as intricate manufacturing processes and automated production lines.