3D printers are revolutionizing manufacturing by making it possible to create complex products quickly and cheaply. 3D printing technology has been around for a while, but it is only recently that it has become affordable for small businesses and hobbyists. This article will explore how 3D printers are changing the manufacturing landscape and what the future of 3D printing might hold.
3D printing technology and its potential.
The 21st century has seen many amazing advancements in technology, one of the most significant being 3D printing. This new technology is transforming manufacturing by allowing products to be made quickly and efficiently. In the past, if a company wanted to produce a new product, it would have to create a mold or prototype, which could be costly and time-consuming. With 3D printing, companies can now create products without any upfront costs or lead time.
3D printing is also changing the way that products are designed. In the past, designers would have to create 2D drawings of their products, which could then be sent to manufacturers for production. With 3D printing, designers can now create prototypes of their products in minutes, which allows for faster iteration and innovation.
3D printing is revolutionizing manufacturing and will have a profound impact on the global economy.
How Do 3D Printers Work?
3D printers work by using a process called additive manufacturing. Additive manufacturing is the process of creating a three-dimensional object by successively adding layers of material until the desired shape is achieved.
This process is different from traditional manufacturing methods, which involve subtractive processes such as machining or carving. With additive manufacturing, businesses can create products with much greater precision and detail.
3D printers have become increasingly popular in recent years, as they have become more affordable and easier to use. Businesses across a wide range of industries are using 3D printing to create everything from prosthetic limbs to car parts.
What are the different types of 3D printers?
Different types of 3D printers use different technologies to create objects. The most common type of 3D printer, and the one most often used in manufacturing, is the additive manufacturing printer. These printers create objects by depositing material layer by layer until the object is complete. Some common materials that can be used with additive manufacturing printers include plastic, metal, and ceramics.
Another type of 3D printer is the subtractive manufacturing printer. These printers work by removing material from a block of material until the desired object shape is achieved. Materials that can be used with subtractive manufacturing printers include metals, plastics, and composites.
Finally, there are also hybrid 3D printers that combine both additive and subtractive technologies. These printers offer the benefits of both technologies and can be used to create more complex objects.
1. Fused Deposition Modeling (FDM)
Fused deposition modeling is a type of 3D printing that is well-suited for prototyping and manufacturing applications. It works by depositing material in layers that are fused together to create the desired 3D shape. The advantage of FDM over other 3D printing technologies is that it can use a wide range of materials, including plastics, metals, and ceramics.
FDM technology is constantly evolving and becoming more widely adopted in manufacturing applications. One recent development is the ability to print multiple materials simultaneously, which opens up new possibilities for creating complex products with multiple functionalities. For example, it is now possible to print a product with a hard outer shell and a soft inner core or to embed electronics or sensors into the product during the printing process.
As FDM technology continues to advance, it is likely to have an increasingly transformative impact on manufacturing.
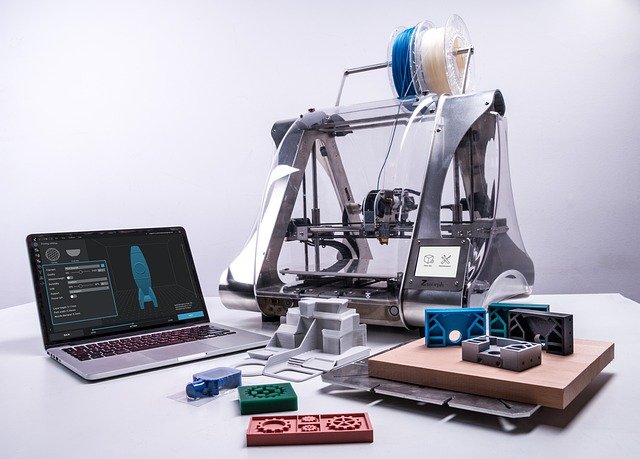
2. Selective Laser Sintering (SLS)
Selective Laser Sintering (SLS) is a type of 3D printing that uses a laser to fuse together small particles of plastic, metal, or ceramic to create a three-dimensional object. The advantage of SLS over other 3D printing technologies is that it can create complex objects with a high degree of accuracy and detail.
SLS is often used for prototyping and manufacturing small batches of parts or products. However, the technology is also being used to create larger objects, such as medical implants and aircraft components.
The future of SLS looks promising, as the technology continues to evolve and become more affordable. With the ability to create ever more complex objects, it is likely that SLS will play an increasingly important role in manufacturing in the years to come.
3. Stereolithography (SLA)
Stereolithography is a 3D printing technology that creates parts by curing layers of photosensitive resin with a laser. SLA printers are typically more expensive than other 3D printing technologies but offer a number of advantages, including high accuracy, fine detail, and a large build volume.
SLA was one of the first 3D printing technologies to be commercialized, and today it remains one of the most widely used 3D printing technologies in the world. SLA-based parts are used in a variety of applications, including medical implants, eyeglass lenses, and automotive components.
The main advantage of SLA over other 3D printing technologies is its accuracy. SLA parts can be produced with tolerances as low as 0.001 inches (0.025 mm), making them suitable for applications where tight tolerances are required.
3D printers in manufacturing: how they are used
3D printers are becoming increasingly popular in the manufacturing industry as they offer a quick and efficient way to produce products.
Prototyping
Prototyping is an important step in the manufacturing process, and 3D printers are making it easier and more efficient than ever before.
With a 3D printer, manufacturers can quickly and easily create prototypes of their products, which can then be tested for form, fit, and function. This allows for faster iteration and development of new products, as well as a reduction in the overall cost of manufacturing.
3D printing is also enabling manufacturers to create customized products more easily. By printing parts on-demand, they can avoid the need for large inventories of stock parts that may not be used. This flexibility gives them a competitive advantage in today’s market.
Customization
3D printing technology has revolutionized manufacturing, giving rise to new opportunities for customization. With 3D printers, manufacturers can produce parts and products that are tailored to the specific needs of their customers. This level of customization was not possible with traditional manufacturing methods.
The ability to customize products has led to a new era of mass customization, in which manufacturers can produce large quantities of customized products quickly and affordably. This is made possible by the fact that 3D printers do not require the same level of setup time and tooling as traditional manufacturing methods.
The benefits of customization are not just limited to manufacturers. Customers also benefit from being able to order products that are specifically designed for their needs. This level of customer service was not previously possible with mass-produced goods.
Overall, 3D printing technology has transformed manufacturing by making customization more affordable and efficient than ever before.
Mass production
In the early days of manufacturing, goods were produced by hand, one at a time. This was a time-consuming process, and it was difficult to produce large quantities of items. With the invention of the assembly line, mass production became possible. This allowed manufacturers to produce large numbers of products quickly and efficiently.
Today, 3D printers are revolutionizing manufacturing. These printers can create complex objects from digital designs. This technology is changing the way goods are produced, and it has the potential to transform manufacturing.
3D printing is faster and more flexible than traditional manufacturing techniques. It enables manufacturers to produce small batches of customized products quickly and cheaply. This is a major advantage for businesses that need to rapidly respond to changes in customer demand.
Reverse engineering
Reverse engineering is the process of taking something apart and understanding how it works in order to recreate or improve upon it. It’s a common practice in manufacturing, and 3D printers are helping to make it more accessible than ever before.
By being able to quickly and easily print out prototypes, manufacturers can rapidly test new designs and iterate on them until they find the perfect solution. And because 3D printers can create complex shapes that would be difficult or impossible to produce using traditional methods, they’re giving companies the freedom to explore new possibilities for their products.
Reverse engineering is an essential tool for keeping manufacturing companies competitive in today’s ever-changing marketplace. With 3D printers becoming more commonplace and affordable, there’s no excuse not to take advantage of this powerful technology.
Quality control
3D printers have the potential to revolutionize manufacturing by allowing for the on-demand production of customized parts and products. This technology is still in its early stages, however, and companies are working to perfect their 3D printing processes to ensure high-quality control.
One issue that must be addressed in order to ensure quality control is dimensional accuracy. This is the ability of a 3D-printed part to match the dimensions of the CAD design. If a part is even slightly different than the intended design, it may not function correctly. To address this issue, companies are using laser scanners and other precision measurement tools to check the dimensions of their 3D-printed parts.
Another challenge with 3D printing is achieving the correct material properties. For example, some plastics may need to be heat-resistant or durable in order to meet certain product specifications.
“Tooling and fixtures”
3D printers are becoming increasingly popular in the manufacturing industry as a way to create prototypes and production-quality parts. One of the benefits of 3D printing is that it allows for the creation of custom tooling and fixtures, which can be used to speed up and improve the quality of production.
In many cases, custom tooling and fixtures can be created faster and more cheaply with 3D printing than with traditional methods. In addition, 3D-printed parts are often more accurate and have a better surface finish than parts made with traditional methods. This means that less time is spent on finishing and assembly, and that final product are of a higher quality.
3D printing is therefore transforming the way in which manufacturing companies create tooling and fixtures, with benefits in terms of cost, time, accuracy, and quality.
The benefits of using 3D printers in manufacturing
A number of industries are already using 3D printers in manufacturing, including the automotive, aerospace, medical, and dental sectors. For example, General Motors has been using 3D-printed parts in its vehicles for years. The benefits of using 3D printers in manufacturing are numerous and varied.
Accuracy
As the world of technology rapidly expands, so too do the capabilities of those within it. Once confined to two-dimensional printing, the introduction of 3D printers has completely changed the landscape of manufacturing as we know it. And while there are still some kinks to be worked out, the accuracy of these machines is constantly improving.
For example, take a company like GE that manufactures parts for both commercial and military jets. In order to create these parts, they need machines that can fabricate them with extreme precision. The smallest mistake could cause an airplane to malfunction, which is why GE spends millions of dollars perfecting its 3D printers.
And it’s not just companies like GE that are benefiting from the accuracy of 3D printers. In fact, any company that relies on manufacturing is seeing an improvement in quality and efficiency thanks to these machines.
Cost-effectiveness
3D printers have revolutionized manufacturing by providing a cost-effective way to produce prototypes and small batch production runs. In the past, companies would have to outsource these services, which was often expensive and time-consuming. With 3D printing, companies can produce prototypes in-house, which saves both time and money.
In addition to prototyping, 3D printers are also well-suited for producing small-batch production runs. This is because there is no need for tooling or molds, which can be expensive to create. With 3D printing, companies can quickly and easily produce the parts they need in the quantities they require.
Overall, 3D printers provide a versatile and cost-effective solution for manufacturing needs. They are perfect for creating prototypes and small batch production runs quickly and easily.
Increased Efficiency
3D printers have revolutionized manufacturing by increasing efficiency and productivity while reducing waste. By eliminating the need for costly and time-consuming tooling, 3D printing has made it possible to produce complex products faster and more affordably than ever before.
In addition to being faster and more cost-effective, 3D printing is also more environmentally friendly than traditional manufacturing methods. Because 3D printing uses less material and energy, it results in less pollution and carbon emissions.
The benefits of 3D printing are already being felt across a wide range of industries, from healthcare to aerospace. As technology continues to evolve, it is expected to have an even greater impact on the way we manufacture products.
Design Versatility
Design versatility is one of the most important benefits of 3D printing technology. With 3D printing, manufacturers can produce parts and products with a wide range of shapes, sizes, and colors. This versatility gives businesses the ability to create unique products that stand out from the competition.
In addition, 3D printing technology offers manufacturers the ability to quickly and easily customize products. This is especially beneficial for businesses that need to frequently update their product designs or produce small batches of custom products. With traditional manufacturing methods, it can be very costly and time-consuming to make even minor changes to product designs. But with 3D printing, businesses can make changes on the fly and produce small batches of customized products quickly and easily.
Overall, the design versatility and customization potential offered by 3D printing technology is transforming the manufacturing landscape.
Environmental Friendliness
3D printers have the potential to be much more environmentally friendly than traditional manufacturing methods. With 3D printing, there is no need for harmful chemicals or large amounts of energy to produce products. Also, 3D printed products can often be recycled or reused, further reducing their environmental impact.
Despite these potential benefits, 3D printers are not yet widely used in manufacturing due to their high cost and limited capabilities. However, as 3D printer technology continues to improve, it is likely that more and more manufacturers will adopt this cleaner and more sustainable method of production.
Accessibility
3D printers have the potential to transform manufacturing by making it more accessible. By making production more accessible, 3D printers could enable small businesses and individuals to create products that were previously only available through expensive and complex manufacturing processes. This could lead to a more democratized and decentralized manufacturing process, which would be more sustainable and efficient.
One way that 3D printers are making manufacturing more accessible is by decreasing the cost of production. 3D printing technology has become increasingly affordable in recent years, with some home 3D printers costing less than $500. This has made it possible for people to produce products at a fraction of the cost of traditional manufacturing methods.
Another way that 3D printers are making manufacturing more accessible is by increasing the range of products that can be produced.
Some challenges to using 3D printers in manufacturing
3D printers are becoming increasingly popular in manufacturing, as they offer a versatile and cost-effective way to produce parts and products. However, there are still some challenges that need to be addressed before 3D printing can be fully integrated into manufacturing processes.
The high cost of 3D printers
While 3D printers have the potential to revolutionize manufacturing, their high cost remains a major barrier to widespread adoption.
A typical 3D printer can cost anywhere from $1,000 to $10,000, and the price of filament (the material used to print objects) can range from $20 to $50 per kilogram. In addition, 3D printers require a significant amount of time and expertise to operate properly.
As a result, only a handful of companies have been able to successfully implement 3D printing into their manufacturing processes. For most manufacturers, the high upfront costs and learning curve associated with 3D printing make it simply not worth the investment.
Until 3D printer prices come down and the technology becomes more user-friendly, it is unlikely that we will see widespread adoption of this transformative technology in manufacturing.
The lack of skilled personnel to operate them
The lack of skilled personnel to operate them is a major challenge facing the adoption of 3D printers in manufacturing. While technology has advanced rapidly in recent years, there is still a shortage of trained operators who can use it effectively. This bottleneck has led to many companies adopting a “training on demand” approach, where they bring in experts when needed, rather than trying to train internal staff.
The lack of skilled personnel is not only for manufacturers but also for the suppliers of 3D printers. Many manufacturers are reluctant to invest in the technology because they cannot find qualified staff to operate it. As a result, the industry is reliant on a small number of specialists who are in high demand and can command high fees.
The limited range of materials that can be used
3D printers have the ability to create objects out of almost any material, including metals, plastics, and even human cells. However, there are still some limitations to what 3D printers can do. For example, most 3D printers cannot print in multiple colors or materials at the same time. Additionally, some materials are too difficult or expensive to print with a 3D printer. As 3D printing technology continues to evolve, it is likely that more and more materials will be able to be printed using this technology.
The slow speed of printing
While 3D printers have the potential to revolutionize manufacturing, their speed is still a limiting factor. It can take hours or even days to print just one item, which is not practical for mass production. Researchers are working on ways to increase the speed of 3D printing, but until that happens, the technology will remain limited in its applications.
The need for post-processing
In the rapidly changing landscape of manufacturing, 3D printers are becoming increasingly popular for their ability to quickly and cheaply produce prototypes and finished products. However, as with any new technology, there is a learning curve involved in using 3D printers effectively. One of the most important aspects of 3D printing is post-processing, which refers to the steps taken after a print is completed in order to improve its quality or function.
Post-processing is often necessary in order to remove supports or smooth out rough edges. It can also be used to add color or other finishes to a print. In some cases, post-processing is essential for the functionality of the final product; for example, printed circuit boards need to be etched before they can be used.
The lack of standardization
The lack of standardization in 3D printing is one of the main obstacles to the wider adoption of technology in manufacturing. Each 3D printer has its own unique set of capabilities and settings, which makes it difficult to replicate results from one machine to another. This lack of standardization also makes it difficult to compare the performance of different 3D printers.
One way that manufacturers are overcoming this obstacle is by using software that can control multiple types of 3D printers. This allows them to create a digital template that can be used to produce consistent results on any machine. Another way manufacturers are dealing with the lack of standardization is by partnering with specific 3D printer manufacturers who can provide machines that meet their specific needs.
The future of 3D printing in manufacturing
The future of 3D printing in manufacturing looks very promising. Technology is constantly improving and becoming more affordable, which is making it more and more accessible to small and medium-sized businesses.
There are already many examples of businesses using 3D printing to create custom parts or products, and this trend is only going to continue to grow. As the technology continues to develop, we will see even more amazing applications of 3D printing in manufacturing.
One of the most exciting things about 3D printing is that it has the potential to completely revolutionize the way we manufacture products. Traditional manufacturing methods are often quite wasteful, but with 3D printing, we can create products using only the exact amount of material needed. This could lead to a huge reduction in waste and a significant decrease in production costs.